An electroplating oil-cooled rectifier is a specialized electrical device used in electroplating processes. It is designed to convert alternating current (AC) power into direct current (DC) power, which is required for the electroplating process. The "oil-cooled" aspect refers to the cooling method used to dissipate heat generated during operation.
Basic Details:
Function: An electroplating oil-cooled rectifier is primarily responsible for rectifying AC power from the electrical grid into stable DC power. This rectified DC power is essential for the electroplating process, where it is used to deposit a metal layer onto a substrate.
Oil Cooling: These rectifiers are often immersed in a cooling oil to dissipate heat generated during operation. The cooling oil helps maintain a stable operating temperature, preventing overheating of the rectifier components.
Applications: Electroplating oil-cooled rectifiers are used in various industrial applications, including electroplating, anodizing, and other metal finishing processes.
Specifications/Additional Details:
Input Voltage: The input voltage of the rectifier depends on the local electrical grid standards. Common input voltages include 208V, 380V, 415V, or 480V AC.
Output Voltage: The output voltage is the DC voltage required for the electroplating process. It can vary depending on the specific requirements of the plating operation but is typically in the range of 0-100 volts or higher.
Output Current: The rectifier's output current capacity is specified in amperes (A) and determines the maximum current it can deliver to the plating bath. Output current can range from a few amps to several hundred amps or more.
Voltage Regulation: Voltage regulation ensures that the rectifier delivers a stable and precise DC output voltage. Tight voltage regulation is critical for high-quality plating results.
Current Control: Some rectifiers provide adjustable current control, allowing operators to regulate the rate of metal deposition during the electroplating process.
Cooling System: The oil cooling system is a crucial component of the rectifier. It may include an oil reservoir, heat exchangers, cooling fans, and temperature sensors to maintain the oil's temperature within safe limits.
Protection Features: Rectifiers often come equipped with protection features such as overcurrent protection, overvoltage protection, and thermal protection to ensure safe and reliable operation.
Control Panel: Many rectifiers have a control panel that allows operators to monitor and adjust various parameters, including voltage, current, and cooling system status.
Efficiency: The efficiency of the rectifier is important as it affects power consumption and heat generation. High-efficiency rectifiers help reduce energy costs and the need for extensive cooling.
Safety: Safety features like interlocks, emergency shut-off switches, and grounding provisions are essential to ensure safe operation in potentially hazardous environments.
Enclosure: The rectifier may be housed in an enclosure made of corrosion-resistant materials, and it should be designed to protect against environmental factors.
Compliance: Ensure that the rectifier meets relevant electrical and safety standards and regulations for your region or industry.
Maintenance: Regular maintenance is necessary to keep the rectifier and its cooling system in optimal working condition.
Cost: The cost of an electroplating oil-cooled rectifier can vary significantly based on its capacity, features, and manufacturer.
#electroplating RECTIFIER #rectifier #plating RECTIFIER #electroplated RECTIFIER #pp TANK #blower #centrifugal BLOWER #pp BLOWER #scrubber #barrel #pp FRP TANK # FUME SCRUBBER # FILTER
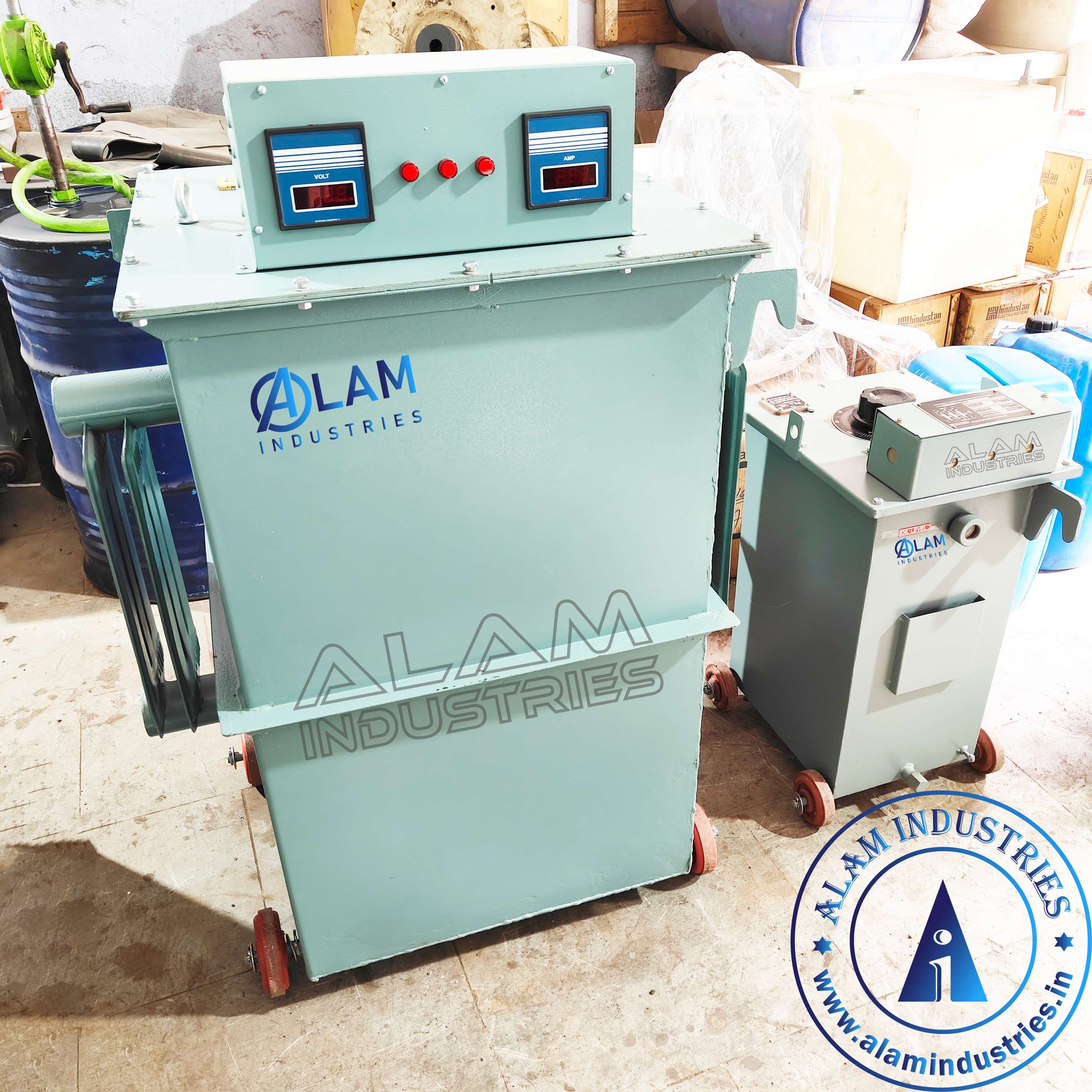